- Home
- Sustainability Report
- Social
- Safety and Quality of Products and Services
- Product and Service Safety as well as the Quality Management
Product and Service Safety as well as the Quality Management
Basic Policy
The Sumitomo Forestry Group will pursue “Zero Defects” and take on the challenge of new initiatives through the implementation of the Sumitomo Forestry Group Quality Policy, a policy for further improving quality in its corporate activities, in order to provide products and services that bring joy to our customers and earn their trust.
All Sumitomo Forestry Group companies and business partners involved in the Group's operations, are required to routinely engage in quality improvement activities as the foundation of corporate management in line with this policy.
The policy reflects the expectations of stakeholders for quality improvement, which were gathered through a questionnaire survey of Group employees on their quality values and activities, as well as interviews with executives, general managers, and major business partners.
In addition to disclosing this policy on the website, we also use various tools to promote understanding and penetration of the policy, such as posting it on posters and including it in the employee handbook.
Sumitomo Forestry Group Quality Policy
Through the pursuit of "ZERO DEFECTS" and the implementation of new initiatives, the Sumitomo Forestry Group seeks to provide reliable products and services that bring joy to our customers.
- Full employee participation in quality enhancement
All employees of our Group operations shall consciously strive to enhance quality with an understanding that our products and services must be of the highest standards. - Improving customer satisfaction
We shall identify quality risks and continuously refine processes and rules to improve customer satisfaction. - Thorough compliance
We shall fulfill customer expectations and strictly comply with all applicable laws, regulations, voluntary standards and other rules. - Promoting digitalization and labor-saving measures
To respond to rapidly changing societal structures, we shall actively promote digitalization and the implementation of labor-saving measures to reduce workloads and raise quality. - Developing human resources who will maintain and enhance quality
Through educational programs related to maintaining and enhancing quality, we shall ensure that our know-how, which is our asset, is passed on to the next generation. - Promoting active communication
We shall effectively utilize our structures and systems to actively pursue communication with our customers and all other stakeholders.
President and Representative Director
Toshiro Mitsuyoshi
Product Safety and Quality Management in the Manufacturing Business
Basic Policy
In response to legal requirements and customer requests, we use PDCA cycles as we work to ensure and improve product safety and quality at each stage of our business activities, from planning and product development to production and sales. Moving forward with continuous improvement is a policy we pursue in our manufacturing operations in order to elevate the quality of the products and services we provide.
Product Safety and Quality Control in the Domestic Manufacturing Business
Initiatives Policy for Product Safety and Quality Control
Sumitomo Forestry Crest has established a quality policy based on ISO 9001 as described below. Each facility and division has formulated specific quality targets and action plans in line with our quality policy, and is committed to maintaining safety and improving quality.
Operating in keeping with the 2015 version of the ISO 9001 quality management system, we strive to elevate quality and service by reinforcing its integration with our actual business operations.
- Click here for related information
Sumitomo Forestry Crest's Quality Targets
Sumitomo Forestry Crest has set the following quality targets for fiscal 2024 based on results of the ISO 9001 top management review.
- Establishment of a certification system for critical process program
- Implementation of risk assessment utilizing QA network*1 management method at the time of launching a new product production line
- Thorough implementation of change point management (4M+3H)*2
- Consideration of additional verification tests at the time of design review and introduction of a mechanism for risk extraction
- Establishment of human resources education system based on TPM*3 activities
- Continued to conduct mutual quality audits by each plant
- Reduction of claims associated with repeated mistakes using 5-why analysis
- Strengthening management system of suppliers and business partners' plants
*1An analysis method to identify which processes can prevent defects and their outflows for each quality assurance item on the production line
*24M is a method for discovering and solving problems by analyzing and improving the four elements of Man, Machine, Material, and Method. On the other hand, 3H is the words taken from the initials of HAJIMETE (first time), HENKOU (change), and HISASIBURI (after a long time), and are used to identify mistakes and other problems from these perspectives and take countermeasures in advance
*3Abbreviation for Total Productive Maintenance. Productive maintenance with all member participation. Management methods for raising productivity in the manufacturing industry
Product Safety and Quality Management in the Housing Business
Basic Policy
Sumitomo Forestry believes that popularizing high-quality, durable houses as social assets plays an important role in creating a prosperous society. Based on this belief, and taking the opportunity of the enforcement of Act on the Promotion of Long-life Quality Housing in Japan in June 2009, the Company formulated a basic policy for product safety and quality control in its housing and construction business in fiscal 2009.
Basic Policy for Product Safety and Quality Control in the Housing Business
- Make houses more reliable by improving their basic functions
- Increase future options for layout to accommodate changes in lifestyles
- Enhance maintenance programs to support long-term upkeep
- Monitor information on any production faults, and share information on handling faults promptly
Sumitomo Forestry offers homes that integrate seismic resistance, durability, better insulation efficiency, Net Zero Energy Houses (ZEH), the promotion of universal design, and easy upkeep to improve all aspects of home performance so as to offer customers homes where they can live in peace of mind and comfort for many years to come.
Product Safety and Quality Management in the Housing Business
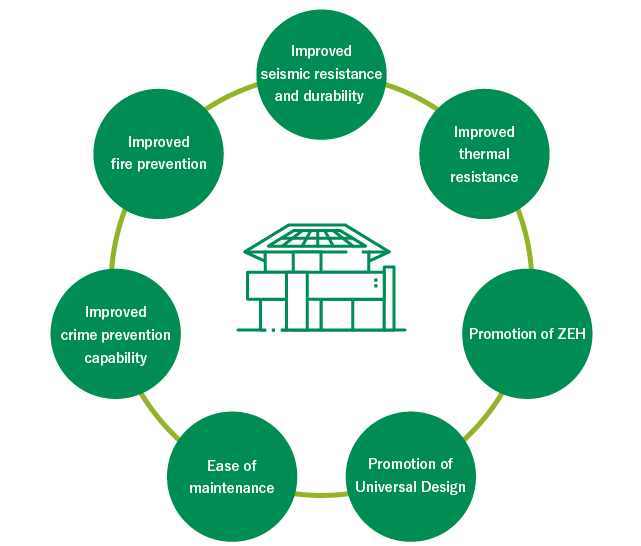
Product Safety and Quality Management in the Construction Business
Basic Policy
Sumitomo Forestry broadly promotes the Construction Business that proposes woodification and use of wood also in nonresidential fields such as offices, medical and welfare facilities, and public facilities. The Construction Business of Construction Business Sub-Division, Global Construction and Real Estate Division, provides high-quality buildings with consideration for user health, safety, and comfort via medium- to large-scale woodification and use of wood, and it obtained the ISO9001 in September 2015 in response to customer expectations. Each plant sets tangible quality targets and a business action plan to attain maintained safety and enhanced product quality.
- Click here for related information
Quality Control in Lifestyle Services Business
Quality Control for Lifestyle Services Business
The Sumitomo Forestry Group's Lifestyle Services Business is expanding a broad range of lifestyle-related services focusing on elderly care businesses and other downstream businesses that support people's lifestyles.
In the elderly care business, Sumirin Care Life and Sumirin Fill Care provide private-pay nursing home and elderly care facilities with nursing care services, as well as in-home services such as day care services and home-visit nursing care.
At Sumirin Fill Care, all employees, regardless of job category, participate in monthly general meetings at each facility to communicate internal initiatives and share residents' situations and challenges.
Sumirin Care Life conducts resident satisfaction surveys. If residents or their families have any requests or comments, we hold a general meeting attended by the director, manager, and station manager. This information is shared at the meeting of persons in charge of services attended by care managers, caregivers, nurses, social workers, nutritionists, rehabilitation staff, etc., and all participants work together to solve problems.
- Home
- Sustainability Report
- Social
- Safety and Quality of Products and Services
- Product and Service Safety as well as the Quality Management