- Home
- Sustainability
- Social
- Occupational Health and Safety
- Occupational Health and Safety Initiatives
Occupational Health and Safety Initiatives
- Rapidly Comprehending and Dealing with Occupational Injury
- Forestry Business Initiatives
- Environmental Energy Business Initiatives
- Manufacturing Business Initiatives
- Initiatives at Construction Sites
- Housing Business Initiatives
- Occupational Safety Initiatives in Construction Business
- Lifestyle Services Business Initiatives
Rapidly Comprehending and Dealing with Occupational Injury
The Sumitomo Forestry Group operates Two-hour Rule system designed to quickly and accurately communicate information to management in the event of an emergency situation that may have a grave impact on company management. In addition to the regular reporting line, it utilizes communication via the division responsible for risk management. Through this system, management can take the best decision speedily, ensuring an initial response which avoids loss and controls the situation. Moreover, it serves a role in collecting and accumulating reported cases and assists in improved business practice and prevention of recurrence.
Furthermore, the structure is organized so that, by sharing information with the public relations departments, important situations are disclosed to stakeholders properly and in a timely manner.
Serious occupational injuries are reported and managed through case reports on risk manifestations at monthly meetings of the Board of Executive Officers, as well as at quarterly meetings of the Sustainability Committee and Risk Management Committee.
- Click here for related information
Countermeasures against Heatstroke
Since 2022, we have been introducing heat prevention watches on a trial basis for employees working at housing construction sites and forests in Japan. When a wearer's core body temperature rises, it alerts the wearer to take a break or stay hydrated, thus avoiding the risk of heatstroke before the wearer becomes unwell. Starting in 2022, the heatstroke-prevention watches were officially introduced for domestic Group companies. Since 2023, a communication-type watch that alerts an administrator at a remote location has been adopted. We analyze trend of alert occurrence and return the information to each department to help prevent occupational injury.
Additionally, from June to August 2024, an on-demand video was streamed to educate employees on heatstroke countermeasures. The video covered essential knowledge, prevention methods, first aid, and real-life examples. It was accessed approximately 500 times.
We will continue to deploy safety education and support measures throughout the entire group to achieve zero work-occupational injury.
Forestry Business Initiatives
Domestic Initiatives
Sumitomo Forestry manages approximately 48,000 ha of company-owned forests in Japan. Contractors conduct planting, appropriately caring for forests, improvement cutting, thinning and clear-cutting operations. For the purpose of preventing occupational injury to these contractors, the Group conducts safety patrols and holds Workplace Safety Conferences at each office twice a year.
At Workplace Safety Conference, we are stepping up educational activities such as lectures by experts in occupational injury prevention and environmental education, and on-site safety instruction.
In fiscal 2024, Workplace Safety Conference were held at least once at each forestry office. At safety conference, we shared various themes with related parties, such as occurrence of forest occupational injuries, occupational health and safety measures in forestry, risk assessment, and prevention of heat strokes, and deepened mutual understanding.
In fiscal 2024, there were no occupational injury requiring payment of compensation benefits for absence from work in accordance with the Industrial Accident Compensation Insurance Act in Sumitomo Forestry's company-owned forests working site. We will continue our efforts to achieve zero occupational injury.
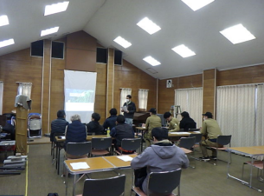
Workplace safety conference (Osaka Forestry Office)
Overseas Initiatives in Forestry Business
The Sumitomo Forestry Group manages a total of approximately 240,000 ha of company-owned plantation forests overseas. To prevent occupational injury, all overseas forestation companies* ensure that operators are equipped with safety equipment, and remind them of safety and health issues through periodic safety lectures and morning meetings.
Specifically, (1) Thorough equipment inspections before work, (2) Regular meetings with logging contractors to evoke caution about safety management and real-time reports in the event of an accident, (3) Assessments of occupational health and safety for the company and logging contractors are conducted by occupational safety experts.
In fiscal 2024, there were twelve occupational injuries (four or more days of lost worktime). As occupational injuries frequently occur when using knives or chainsaws for clearing underbush, we have taken steps to prevent recurrence by promoting safety education for workers, reviewing work methods, and introducing protective equipment.
*Open Bay Timber Ltd. (OBT), PT. Wana Subur Lestari (WSL), PT. Mayangkara Tanaman Industri (MTI), PT. Kubu Mulia Forestri (KMF), PT. BINA OVIVIPARI SEMESTA (BIOS), Tasman Pine Forests (TPF)
Environmental Energy Business Initiatives
In addition to safety patrols by employees, the Environment and Energy Department and the Quality Control and Worker Safety Management Department conduct annual internal audits at the fuel chip plant of the Environment and Energy Business to prevent occupational accidents for employees and business partners who enter and leave the plant. Improvements and corrections are made at the work site.
In fiscal 2024, there were two instances of occupational injury requiring payment of compensation benefits for absence from work in accordance with the Industrial Accident Compensation Insurance Act at the work sites of our environmental and energy business. As a result, with the contractors involved, response measures to prevent recurrence were discussed and agreed. Additionally, warnings were issued to other contractors through the Workplace Safety Conferences.
Manufacturing Business Initiatives
Sumitomo Forestry Crest
Sumitomo Forestry Crest's Occupational Health and Safety Policy is to provide its employees and subcontractors with a workplace environment that aims for "Zero Accidents to Zero Hazards." To accomplish this, we are working to develop a system that allows all employees to make continuous improvements, and employees at each plant proactively report near-miss incidents (863 reports from 515 employees in fiscal 2024) to the Health and Safety Committee, as well as other small group activities (TPM activities) in the workplace to exchange opinions and implement the PDCA process. Management cycle of PDCA is used to improve the efficiency of manufacturing activities while reducing risk.
In fiscal 2024, there were three lost-time injuries (one involving four or more days of leave and two involving one to three days), three non-lost-time injuries, and one accident involving a contractor at a business site. Based on the fundamental concept of "Safety First," the Sumitomo Forestry Group will continue to strive to create a thriving workplace by improving a healthy and safe workplace environment.
Safety Objectives
- Zero occupational accidents
- Zero fire accidents
- Zero traffic accidents
- Zero risks assessed at Level III or higher (on a five-level risk assessment scale)
- Improvement of safety awareness of site workers
- Safety measures for machinery and equipment
- Thorough risk assessment
Identification of hazard sources / effective risk reduction countermeasures (foolproof) / residual risk control - Safety education to increase risk sensitivity
KYT / Hierarchical Safety Education / Safety Experience Training Seminar / Certification and Specialized Training - Full employee participation in health and safety initiatives
Discussions at OHS Committee / Safety Patrols / Sort out response measures in case of accidents / Evacuation Drills
- Safety Objectives
- Target for Priority Management
- Policy to Achieve Targets
Safety and Health Improvement Activities, etc.
Regular workplace safety patrols are conducted at each Sumitomo Forestry Crest plant to identify risks and make improvements. Near-misses and risk assessments are conducted on some of the identified risks, which are then deployed to other departments and basic safety measures are adopted to prevent accidents.
Risk assessments are conducted whenever new equipment is introduced or production lines are changed, with the aim of preventing employee hazards and health problems. We seek to ensure workplace safety by evaluating potential hazards in equipment and operations and implementing measures to reduce the risk level.
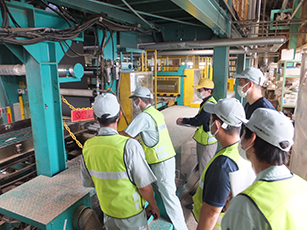
Mutual safety audits between plants
From the analysis of workplace accidents that have occurred, it was observed that some accidents were caused by a lack of safety precautions as a result of acts that were not expected in ordinary work, and were not identified as potential sources of danger. It is vital to identify hazard sources from various perspectives and increase sensitivity to hazards to recognize potential dangers.
In recent occupational accidents, many of the most serious incidents have occurred during forklift operations and work involving rotating equipment such as rollers and blades. As a result, we are focusing our improvement efforts on these two types of operations.
Since December 2020, we have been holding monthly safety countermeasure review meetings. In addition to the soft measures we have implemented to date, such as safety training, we are also considering physical (hard) measures, including adjusting the volume of forklift buzzers, separating pedestrian and vehicle pathways, and installing safety covers on rotating equipment and emergency stop devices such as safety mats. These efforts aim to create a safer work environment.
Sumitomo Forestry Crest is engaged in TPM* activities. All factory employees, without exception, have a role to play and are involved in the activities through 3 basic activities -"All Member Participation", "Voluntary Conservation", and "Zero Loss". One of our main objectives is to achieve zero occupational injury by implementing safety activities such as "Hiyari-Hatto" prevention (near miss) and safety patrols, etc., and we are working toward this goal on a daily basis.
*Abbreviation for Total Productive Maintenance. Production and conservation with all member participation. Management methods for raising productivity in the manufacturing industry
Sumitomo Forestry Crest Co., Ltd. conducts mutual safety audits at each plant. In fiscal 2024, we held two audit at each plant to confirm observance of rules such as wearing of protective equipment by on-site workers, as well as sufficient ability and training for work and implementation of risk assessment.
Overseas
The Sumitomo Forestry Group's overseas manufacturing companies strive to create and maintain a safe and healthy workplace environment under the basic idea of "Safety First", and are united under the basic policy of "creating manufacturing sites with respect for human life and commitment to safety first". In particular, we are developing activities focusing on risk assessment and risk prediction training (KYT), as well as sharing examples and activities among plants to achieve a safe workplace environment for the entire company.
Safety Objectives
In our overseas manufacturing companies, we are promoting a culture of respect for human life and safety-first manufacturing sites under the fundamental policy of "safety takes precedence over all else." In fiscal 2025, we continue to position the elimination of accidents involving rotating machinery -which account for a large portion of occupational injuries resulting in four or more lost workdays -as a key priority, while also strengthening efforts to prevent fires as part of our commitment to occupational safety activities.
Occupational Health and Safety Initiatives
The following are the details of the priority initiatives.
(1) Elimination of work-related accidents involving rotating machinery
We are reviewing past occupational accident cases and working to eliminate accidents involving rotating machinery -such as entanglement in rotating rollers or lacerations from rotating blades -which frequently account for incidents resulting in four or more lost workdays. Each factory is identifying machinery with rotating components, assessing associated risks, and implementing both physical and procedural safety measures. These include installing safety covers and fences, ensuring equipment is shut down during maintenance, managing lockout/tagout procedures, and providing relevant training.
(2) Revision and enforcement of fire prevention management procedures
In response to recent cases in Japan of occupational accidents with more than four lost workdays occurring at wood processing factories, we are strengthening fire prevention efforts at our Group manufacturing facilities. We share examples of major fire incidents at peer companies and minor fire incidents within our Group to raise awareness about fire risks. In addition, the Head Office regularly monitors the status of fire prevention procedures to ensure they are being properly maintained and followed.
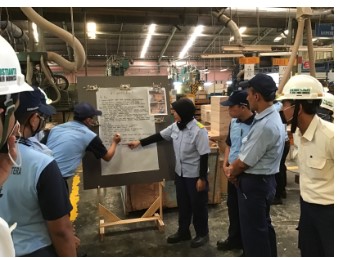
Risk prediction training for local employees at Indonesian manufacturers
Initiatives at Construction Sites
Sumitomo Forestry prioritizes occupational health and safety above all else on housing construction sites. Therefore, we raise awareness about occupational health and safety information and important items about safety in employees of the Sumitomo Forestry Group and also every worker involved with Sumitomo Forestry homes, such as on-site construction contractors.
In fiscal 2024, we conducted "Eliminating Occupational Injury Campaign 2024." Purpose of this campaign is to ensure that all employees share a strong commitment to never causing an accident this fiscal year. We asked for safety slogans from the Production Group, building contractors working at our sites under the theme of "Elimination of Five Major Disasters (Falls, Tip-overs, Accidents with Tools, Accidents with Heavy Equipment and Heatstroke)." Outstanding entries were featured in a daily tear-off calendar, with 7 selected from the Production Group, 13 from homebuilders, and 11 from building contractors -for a total of 31 slogans. The calendars were distributed to each branch office and primary building contractor.
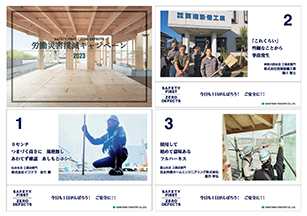
"Occupational Injury Elimination Campaign 2024" daily calendar (part)
The Occupational Health and Safety Policy for fiscal 2024 is "Safety First." In addition, we incorporated the slogan "STOP Five Major Accidents!" in Our Values. Based on injury trends and analysis of previous fiscal year, we have established "Priority Management" section to focus on specific activities. In order to ensure thorough compliance and management of safety standards for each process, we are working to eliminate occupational injury by predicting risks before starting work and promoting elimination of risks and safety assurance.
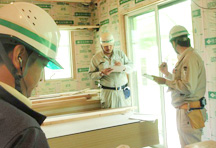
Safety check at construction site
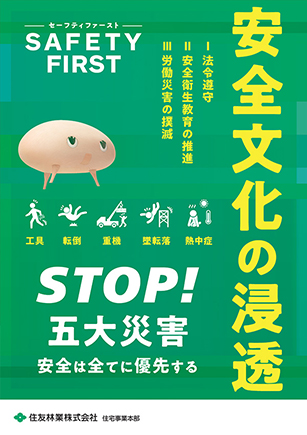
Safety standards poster
Housing Business Initiatives
The Housing Division is implementing various measures to eliminate occupational injuries.
At the beginning of the fiscal year, branches, offices, and cooperative building contractors prepare an "Annual Plan for Safety, Health and Environmental Management". Based on items for enhanced risk assessment, this plan is implemented and managed in a planned manner throughout the year, including occupational health, safety and environmental conferences, regular occupational health and safety conferences, special safety patrols, and safety guidance.
In the event of an occupational injury, we are required to make a first notification to all parties concerned within two hours of the occurrence and prepare an accident report by the next day. In addition to injury prevention conferences after collecting related persons within 7 days, hearing and detailed investigation, and effective countermeasures should be planned and executed by using 4М analysis* and risk assessment to prevent similar injury. In addition, after an accident occurs, the headquarters prepares a preliminary report on the accident, which includes measures to prevent recurrence, and disseminates it to the contractors concerned and workers under its jurisdiction at regular safety and health council meetings and on-site safety meetings.
As one of the measures to promote DX at construction sites, "in-out auto (beacon)" was introduced in April 2022 to automate entry/exit records at construction sites. By changing entry and exit records from manual to automatic, we are able to eliminate record omissions and errors and to accumulate more accurate work history. At the same time, the system reduces the burden on workers to record their entry and exit, and distributes useful information to them when they enter, thereby improving work efficiency and ensuring safe operations.
*A method of thinking about things in terms of four elements: people (Man), machinery and equipment (Machine), work, environment and media (Media), and management (Management)
Image of "in-out auto (beacon)" operation
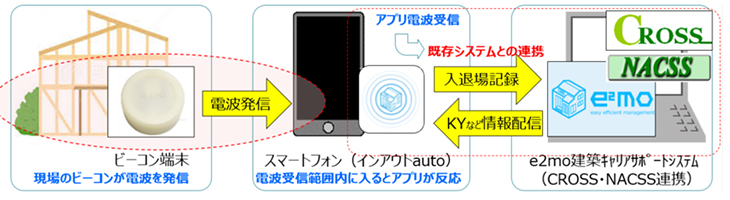
Association of Sumitomo Forestry Safe Building Contractors
Association of Sumitomo Forestry Safe Building Contractors aims to prevent occupational injuries and fires at construction sites, improve work efficiency and the welfare of victims, and enhance quality, while contributing to the development of members' businesses by improving technology and management skills of construction and deepening friendship and exchange among members.
The group is chaired by the Divisional Manager of the Housing Division of Sumitomo Forestry, and its members include Group companies Sumitomo Forestry Home Engineering and Sumitomo Forestry Landscaping, as well as 63 branches (as of June 2024) of construction companies throughout Japan. In addition, safety, health, and environmental conventions are held at each branch during the fiscal year, and lecturers are dispatched from the headquarters to give safety lectures. The content of the lectures is to raise awareness of occupational health and safety by explaining the Sumitomo Forestry Group Occupational Health and Safety Policy and the Housing Division Health and Safety Management Policy, explaining key measures, the Company's roles and responsibilities under laws and regulations, accident statistics, and accident case studies.
Annual Plan for Safety, Health and Environmental Management
At the beginning of each fiscal year, the Housing Division prepares an "Annual Plan for Safety, Health and Environmental Management" for each branch and office. Based on the risk assessment enhancement items, we systematically implement and manage safety, health, and environmental conferences, regular safety and health council meetings, special safety patrols, safety guidance, and other activities throughout the year. We are also examining physical countermeasures, such as separating the traffic lines of construction site workers and pedestrians, to create a safer work environment.
Safety Training for Construction Contractors
The Housing Division publishes monthly Safety, Environment and Quality Inspection Department Information that includes information and topics about occupational health and safety as well as the environment to help prevent accidents and avoid risks by repeatedly raising awareness at branches and construction contractors.
Sumitomo Forestry conducts safety training throughout Japan by visiting building and demolition contractors. We conduct special education and safety and health education to provide direct guidance to workers at the site, and promote efforts for safety and environment at the site by helping them understand the concept of "awareness of a safety culture."
Branches hold safety and health conferences defined by law every month, and give guidance to improve safety awareness and knowledge of contractors, such as confirmation and improvement guidance of site conditions by occupational health and safety patrol of the site.
Occupational Safety Initiatives in Construction Business
The Construction Department of the Construction Business Sub-Division, Global Construction and Real Estate Division, reviewed its safety procedures in an effort to further enhance safety and quality. By identifying safety and environmental risks in greater detail before construction begins and implementing thorough preventive measures, the department aims to ensure safe and high-quality worksites.
Lifestyle Services Business Initiatives
The Sumitomo Forestry Group's Lifestyle Services Business covers a broad range of lifestyle-related services focusing on elderly care businesses and other downstream businesses that support people's lifestyles. Apart from the elderly care business, the Group also operates insurance and solutions business, lodging and community revitalization business, and a golf course management business.
Initiatives in the Elderly Care Business
In the elderly care business, Sumirin Care Life and Sumirin Fill Care provide private-pay nursing home and elderly care facilities with nursing care services, as well as in-home services such as day care services and home-visit nursing care.
Conference of OHS Committee is held monthly at each site to ensure the safety of both users and employees. In the event of an accident, meetings are held at each site to discuss the details of the accident, causes, analysis, and measures to prevent recurrence, which are then reported to the headquarters of each company for deployment to all sites. In addition, Sumirin Fill Care's "Manual of Care Operations" explains our values and risk management for caregivers.
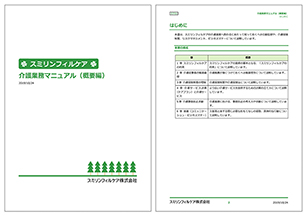
Sumirin Fill Care's "Manual of Care Operations"
Main Risk Reduction Measures for Elderly Care Business
Back Pain Prevention
In addition to distribution of back pain belts to new graduates to prevent back pain, which frequently occurs at nursing care sites, Sumirin Fill Care is working to prevent back pain among employees who are unfamiliar with nursing care.
Additionally, a Fitness Gym Subsidy Program has been introduced to promote both back pain prevention and improved health literacy. The company has corporate contracts with fitness service providers and covers membership and annual fees, as well as a portion of monthly fees.
At Sumirin Care Life, all facilities are equipped with bathing devices that incorporate fine bubble technology. This technology helps reduce the need for caregivers to bend down, thereby preventing lower back strain. In addition to back pain prevention, it also contributes to improved skin quality for residents.
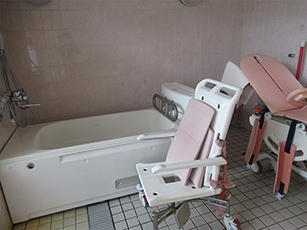
Shower bathing device (fine bubble technology)
Reduction of Fatigue Due to Night Shift Work
Each company adjusts life rhythm and maintains health of staff who works at night, for example, day after night shift is generally set aside as a day off, and time for napping is ensured during the night shift.
Reduction of Risk to Residents
At Sumirin Care Life, we conduct three daily hand-offs regarding changes in residents' physical condition, and we also hold an all-staff conference once during the day to share information. At Sumirin Fill Care, we share information regarding changes in residents' condition through intercom devices and medical records, to establish a system for preventing our staff from overexerting themselves which can lead to accidents. The residents' physical conditions and the status of discharge are also posted in the office to visually grasp the situation.
Initiatives in the Golf Course Management Business
Takinomiya Country Club, a golf course operated by Kawanokita Development, displays "Safety Month Banners" in the clubhouse and other locations twice a year during Safety Month, and all staff members wear "Safety Month" patches to ensure the safety of staff and golf course visitors during this period.
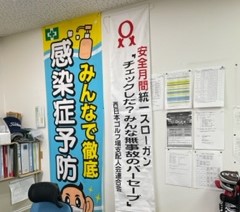
Safety Month Banners
Major Risk Mitigation Measures in the Golf Course Operation Business
At Takinomiya Country Club, the course managers and caddies wear vests with blowers to prevent heat stroke in summer. To prevent heat stroke among customers, we have installed a shading sheet in the starting room that can block 70% of sunlight, and we provide rehydration tea during play.
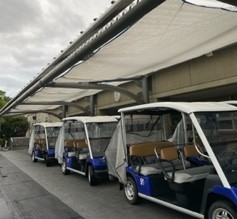
Shade sheet in the start room
Initiatives in the Insurance and Solutions Business
Sumirin Enterprises, which operates insurance and solutions business, distributes Mitsui Sumitomo Insurance's information magazine "Tips for Safe Driving" to all employees once a month by e-mail to prevent traffic accidents.
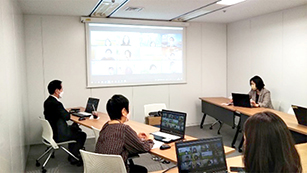
OHS Committee
Securing Safety with State-of-the-art Technologies and Labor-saving Measures
Sumirin Fill Care and Sumirin Care Life, which operate nursing care businesses, have introduced medication support systems to prevent accidents caused by medication errors. When staff of facility gives medicines to residents, we use a mobile terminal to check possibility of wrong person, wrong date and time, and double medication, which are highly likely to occur due to human error.
Both companies have introduced ICT monitoring systems in all of their facilities, enabling real-time monitoring of residents' sleep conditions and changes in their physical condition, especially during the nighttime hours. As a result, the system is able to provide oversight in lieu of regular nighttime patrols, allowing the company to focus on those in need of assistance, thereby reducing the workload during the nighttime hours.
Sumirin Enterprises, which uses vehicles for its insurance and solutions business, uses telematics, an internet-connected vehicle operation proxy system, to ensure safe driving. Sudden acceleration, sudden deceleration, speeding, etc. will be emailed to the supervisor, and the supervisor will instruct the driver if there is a risk of danger. In conjunction with the start of installation of drive recorders, we are working to deter traffic accidents.
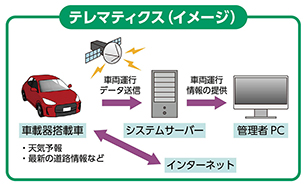
Telematics (image)
- Home
- Sustainability
- Social
- Occupational Health and Safety
- Occupational Health and Safety Initiatives